Automated Quality Inspections: the Promise and the Potential of Optimization
Choosing the right components for the task at hand boosts accuracy, reliability, and usability, all while minimizing costs.
As the transition to Industry 4.0 has gained momentum, you and your competitors strive to eliminate subjectivity from production processes by deploying automated quality inspections (AQI). AQI takes the guesswork out of quality checks, giving you the ability to better understand your production process, ensuring reliability and excellence. AQI is available in different forms. Each AQI solution utilizes a variety of visual detection technologies and data processing techniques, producing wide variations in accuracy, reliability, usability, and cost. Consequently, your AQI could be causing unnecessary expenses due to prolonged runtimes, extended training requirements, and poor data processing. To avoid being held back by technological mismatches, it’s important to optimize your AQI for the problem it’s meant to solve.

THE USE AND TYPES OF AQI
Despite the variability of uses, the fundamental problems that AQI seeks to solve are universal — to address the slow and unreliable manual inspections that result in high labor costs. Workers cannot inspect every product; they can only check a sampling. As assembly procedures and products grow more complex and business owners seek to stay competitive by boosting assembly speeds, these workers create a bottleneck and allow defective products to reach consumers. Deploying an AQI is a great way to overcome these pain points. The technology is extremely flexible, with automated optical inspections being used across industries, including automotive and aerospace production, medicine, and food.
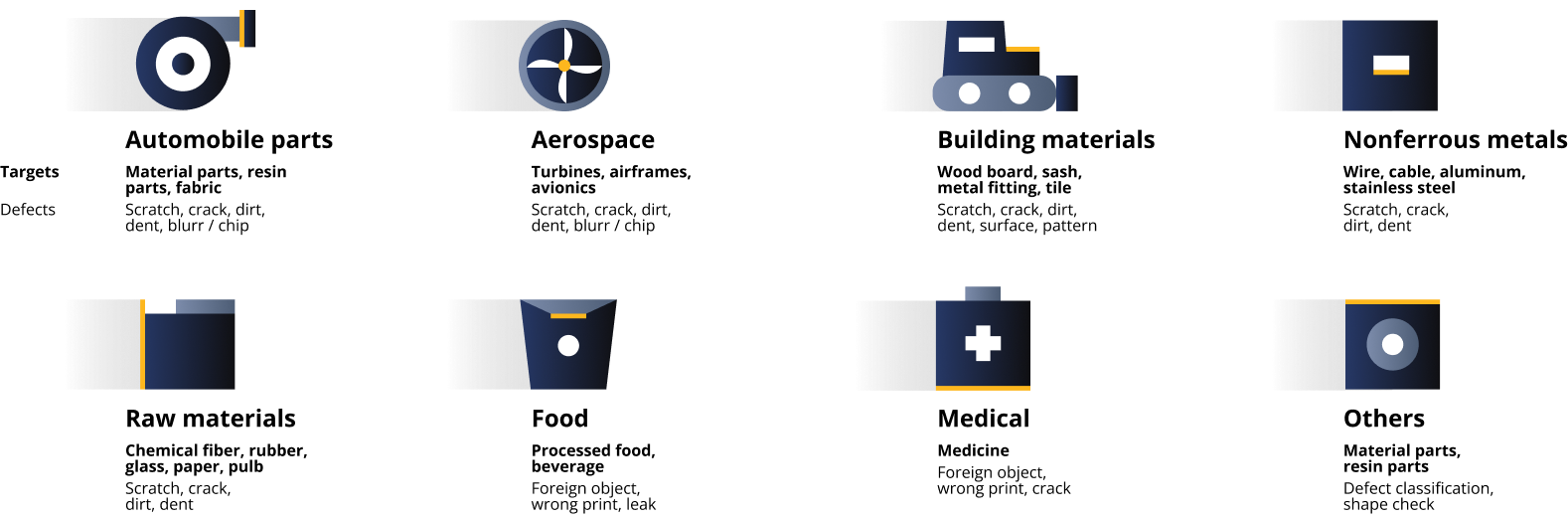
Different applications have different requirements that must be considered. For instance, verifying the print in food production doesn’t require submillimeter accuracy. However, that granularity matters if you're inspecting medical equipment where even the smallest defect can cause failure. Similarly, when monitoring for corrosion on an oil rig, looking for defects is essential. But when analyzing the quality of a product’s final assembly, finding misalignment of components or incorrect fits between exact parts is required.
With that much variance, it only makes sense that your AQI should be tailored to its purpose.
That may seem intuitive, but unsuitability nonetheless runs rampant. To a large extent, that is due to one culprit: an overreliance on flashy technologies to complete jobs that simply don't require them.
NEURAL NETWORKS VS. CLASSICAL COMPUTER VISION
There is considerable buzz around artificial intelligence (AI), and AQI is no exception. AI, in the form of deep neural networks, has its place in AQI. However, if your main business goal is a fast and accurate inspection for a manufacturing pipeline, AQI might not be the right choice. While neural network-based visual classification and detection technologies can offer high accuracy, they require large amounts of training data and extended training times. In the end, the purported payoff comes in the form of high accuracy, but if you are inspecting things with a large degree of uniformity, that extra power isn’t needed. Classical computer vision, on the other hand, can be deployed quickly and has lower processing costs. That might be more important to you if time is of the essence.
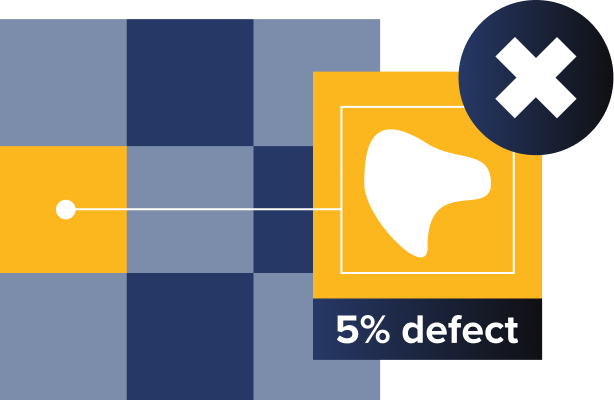
Aside from deployment speed, the accuracy produced by neural networks can be achieved with computer vision without making trade-offs in other areas. The key is to strategically deploy each technology, taking full advantage of the benefits of each. And if you haven't yet investigated these options, you might be paying for unnecessary technology that is impeding your operations.
BEHIND THE SCENES WITH YOUR AQI
To get to the bottom of whether your visual inspection is using an inefficient technology stack, it's critical to interrogate precisely what you want it to do. That will affect both your hardware and software and will require extensive fine-tuning.
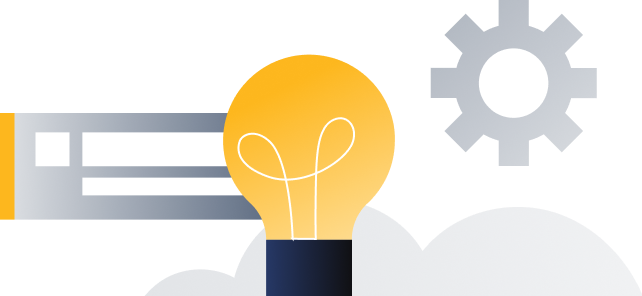
That type of finesse is what we were able to provide for numerous business cases from food package inspections to automotive assembly quality assurance. Each case has its own level of complexity and requires specific approaches. Nevertheless, the problem can be divided into two separate issues: object detection and anomaly detection.
Although these two aspects of AQI are interrelated, they have different implementation requirements. If you want to start streamlining or creating your own AQI solution, let’s talk.
In the meantime, we invite you to read our white paper on custom-fitting your AQI solution to your needs, while also saving time and money in the process.