Exploring the Potential of Physics-Informed Neural Networks
Physics-informed neural networks are a potential game changer in artificial intelligence. Integrating fundamental physical laws into the machine learning process enables PINNs to tackle complex problems where traditional data-driven models often fall short.
Let's discuss some of the ways PINNs are reshaping AI solutions.

What are PINNs?
PINNs embed physical laws into the machine learning pipeline, making them valuable for solving complex problems where traditional data-driven models may struggle. PINNs can be incorporated into all the model steps, this includes problem selection, curating data for architecture design, and loss function creation and optimization, ensuring that the model respects the relevant physical laws.
What problems do PINNs solve?
PINNs are particularly beneficial in scenarios where data may be scarce, noisy, or expensive to obtain, as they allow the model to leverage physical laws to make accurate predictions or simulations with less reliance on extensive data.
Common use cases for PINNs can be categorized into three buckets:
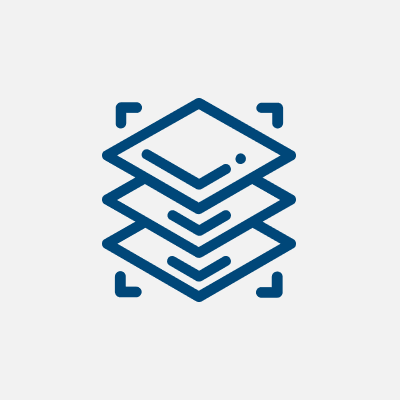
Static data (simulated or experimental):
Fluid dynamics experiments capture the flow around objects, informing models.
An electrical grid system's static load is modeled to optimize energy distribution and forecast demand.
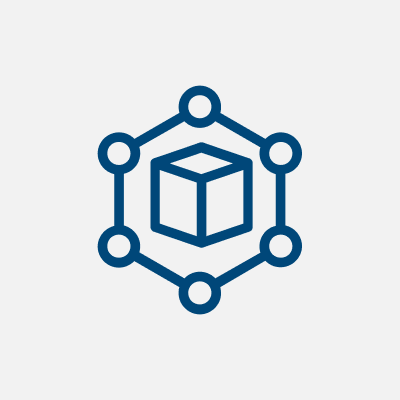
Living and physical (cyber-physical experiment):
Robotic arms used in manufacturing must respond to dynamic environments and execute precise movements.
Drone systems that require real-time adjustments to maintain stability and navigate environments.

Interactive data (simulated only):
Interactive simulations are used in video game physics engines where the environment responds to user inputs in real time. This is an inevitable part of video/3D object AI generation and can improve physical realism in VR/AR.
Real-time simulations of fluid interfaces, such as those encountered in oil and water separation processes, are simulated.
Simulate and predict the aerodynamic performance of turbine blades under varying wind conditions.
What tools exist for PINNs?
What are the three PINN use cases SoftServe R&D works with?
1. Virtual flow-metering of ESP oil wells
With electrical submersible pump technology dominating the current artificial-lift oil extraction landscape, flow-metering of ESP oil wells becomes a critical task. However, obtaining reliable flow rate measurements proves challenging due to the high cost and technical limitations of physical equipment, which calls for the development of novel soft-sensing approaches.
To address this issue, SoftServe designed a hybrid PINN-based virtual flow meter, where the knowledge of underlying physics is combined with auxiliary sensor data to yield accurate flow rate estimates. Compared to more traditional methods, this solution operates over a wide range of parameters and can be used for different wells without any need for retraining. Our VFM application can serve as a foundation for comprehensive digital-twin models of upstream oil production systems.
2. Heat sink design optimization
Optimizing heat sink configuration to ensure the undisrupted and efficient operation of computer hardware systems relies heavily on resource-demanding and time-consuming multiphysics simulations. Our PINN-driven solution for heat sink design leverages the approximative power of neural networks to simultaneously solve conjugate heat transfer equations over wide ranges of heat sink geometry parameters.
This key advantage of the PINN approach allows us to cover the entire design space in a single training, promising to alleviate intractable computational requirements and speed up the simulation process. Based on the obtained PDE solutions, optimal configuration satisfying predetermined design criteria is determined by minimizing temperature on a chip.
3. Chemical reactor
A global oil and gas company was looking for a PINN-based solution to model microkinetics and optimize the “throughput” of a chemical reactor based on operating conditions.
A joint team from SoftServe and the client used PINNs as a part of a hybrid model for a chemical reactor running the Fischer-Tropsch process. This included two aspects: using a PINN to solve a nonlinear equation describing the dependence of reaction rates on the conditions and using another PINN to model the distribution of reactants inside a catalytic pellet by solving appropriate physics-based differential equations. The implementation was done within the NVIDIA Modulus framework.
The PINN-based model enabled a speedup of up to 106 times in the computation of target quantities when running on GPU, in contrast to conventional CPU-ported solutions. Moreover, the differentiability of the PINN model allows its application in higher-level optimization workflows, such as reaction condition optimization.
4. Molecular electronic potential
Predicting the distribution of the electronic density in chemical compounds is one of the cornerstone problems in material science. Conventional quantum-chemical approaches are computationally intense, while physics-based AI models help reduce the needed resources.
We designed a custom predictive pipeline with physics-based loss to produce a spatial distribution of molecular electrostatic potential. This approach reduces model complexity due to parameter-efficient training, while rotational and translational symmetries (equivariance) are maintained by design.
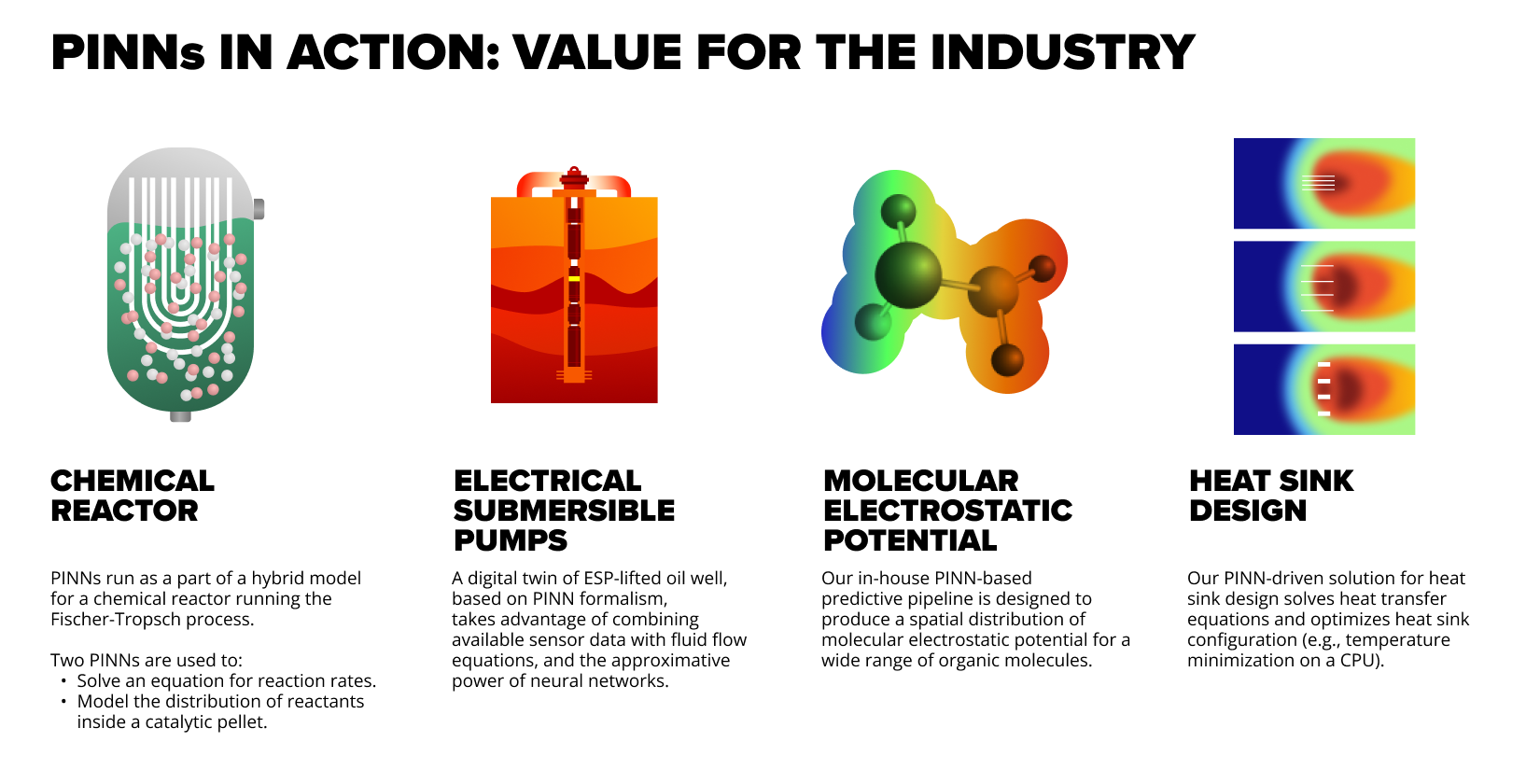
SoftServe showcased a PINNs solution at the NVIDIA GTC 2024 conference. Our presentation highlighted the application of physics-informed machine learning and NVIDIA Modulus for Virtual Metering in ESP Oil Wells. We're excited to share the poster presentation with our audience.