How Moving Toward Industry 5.0 Can Help Manufacturers Deliver Even Smarter Outcomes
When your responsibility is to make your customers more competitive, it is vital to stay ahead of the curve. Nowhere is this more important than in the manufacturing sector, where it is critical to deliver better outcomes in global supply chains, logistics, automation, and engineering solutions. Success in those areas will enhance operational efficiency, reduce costs, and improve product quality.
But sometimes even the best need additional specialist skills to be even better, particularly those that supply the backbone infrastructure and processes that make manufacturers work. That’s why SoftServe has already done the heavy lifting to develop a comprehensive framework that enables organizations to smoothly move from Industry 4.0 toward the much more agile Industry 5.0.
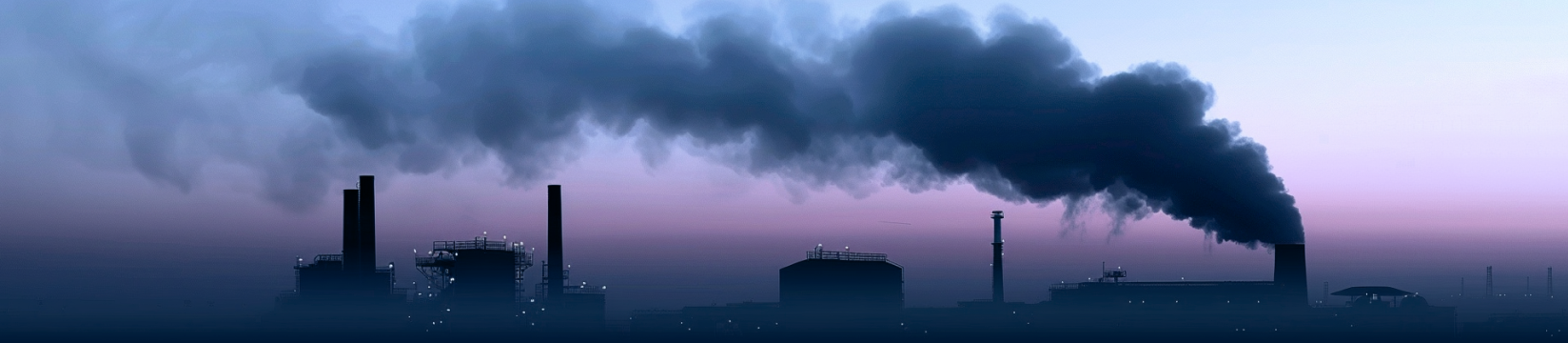
Future profitability
That is why securing the future profitability and reliability of manufacturing operations requires an interwoven approach of technical and business acumen to benefit businesses and their customers.
In this evolving landscape of manufacturing, moving towards Industry 5.0 is going to be a crucial element of staying competitive. Industry 5.0 has at its foundation a human-machine collaboration that blends advanced technologies with human-centric solutions to deliver more informed decision-making and greater agility in an integrated ecosystem.
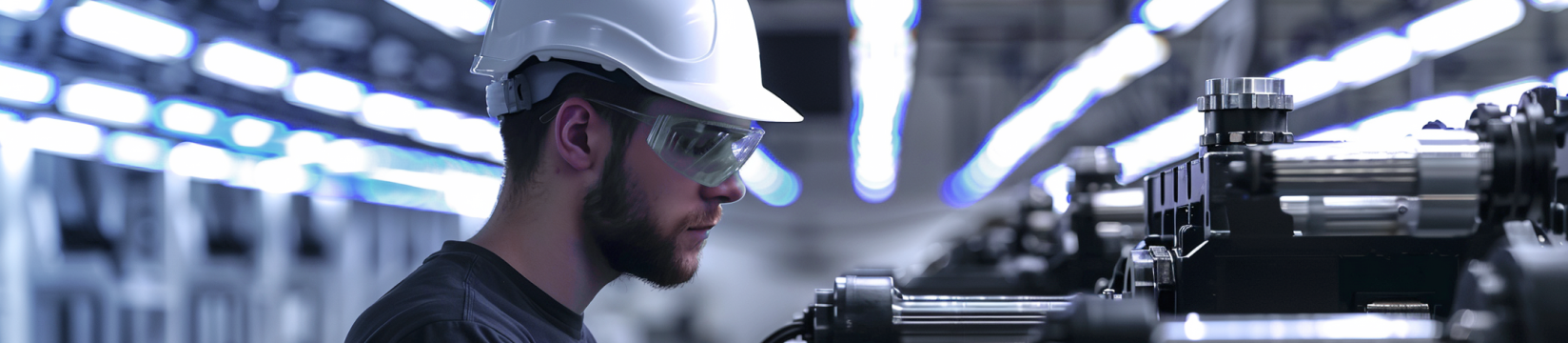
Workforce augmentation
Much of the manufacturing narrative when discussing new technologies such as AI and ML has been around the reduction of human roles and their replacement with machines. Yet, by equipping workers to increase productivity using automation and advanced tools, technology can expand normal human capabilities and reduce non-value-added activity.
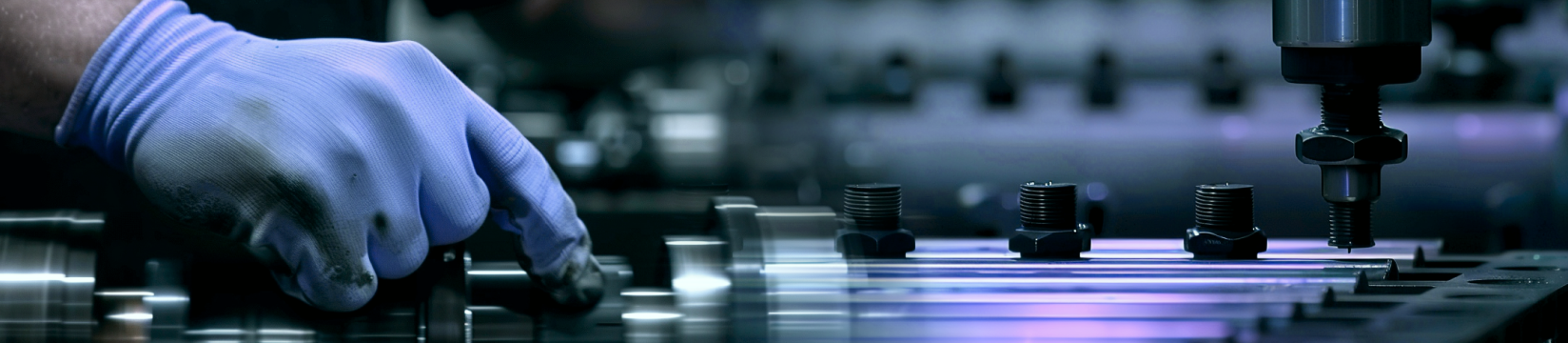
Labor and workflows
Many of the biggest challenges manufacturing businesses face are linked to rising costs. These include addressing labor shortages, finding qualified labor, and upskilling current workforces. But in order to overcome these hurdles they will need to understand how to leverage AI and advanced technology that will automate tasks and increase worker productivity.
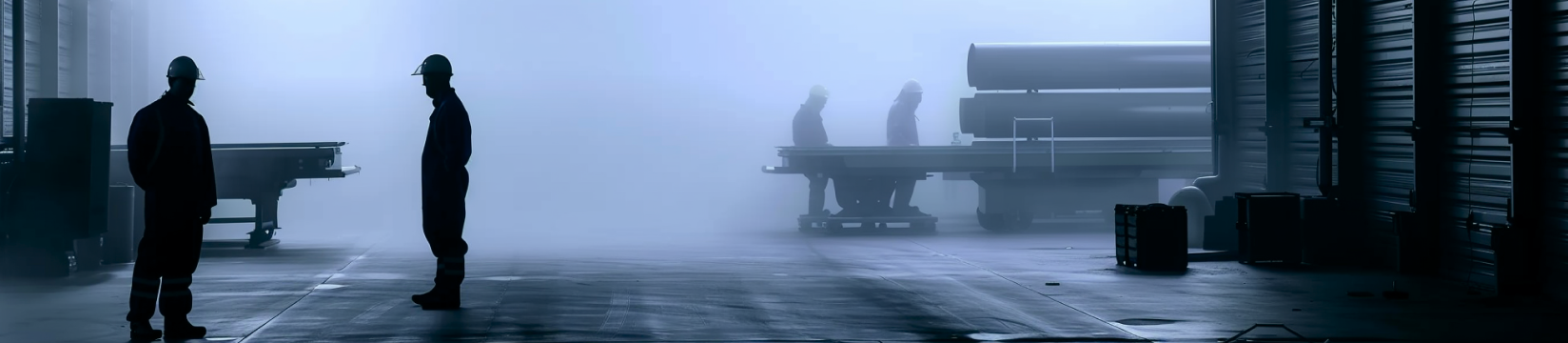
One of the first steps towards tackling this is understanding how companies become more competitive when using AI, ML, IoT, and machine data. It means integrating these technological tools into existing workflows and using them to provide real-time guidance and support.
Manufacturers will then be able to develop AI-driven applications that support workers in complex tasks, reducing cognitive load and errors — providing the ability to gather and analyze data from machinery using LLMs, to identify defects and anomalies.
AI-driven applications will enable businesses to fine-tune equipment operating parameters and define the ideal settings with real-time adjustments to prevent output deviations. By using a combination of emerging automation and digital technologies, Industry 5.0 solutions can ensure process control traceability and predictability.
Automation
The next step to achieving greater efficiency is ensuring wider levels of automation. LLMs can help automate repetitive tasks such as data entry, as well as gathering and analysing large amounts of data from numerous sources. It can also mitigate risks in dangerous and complex tasks by helping to implement monitoring systems that detect and address unsafe behaviours in real-time. It creates a predictable, self-correcting environment across the factory floor.
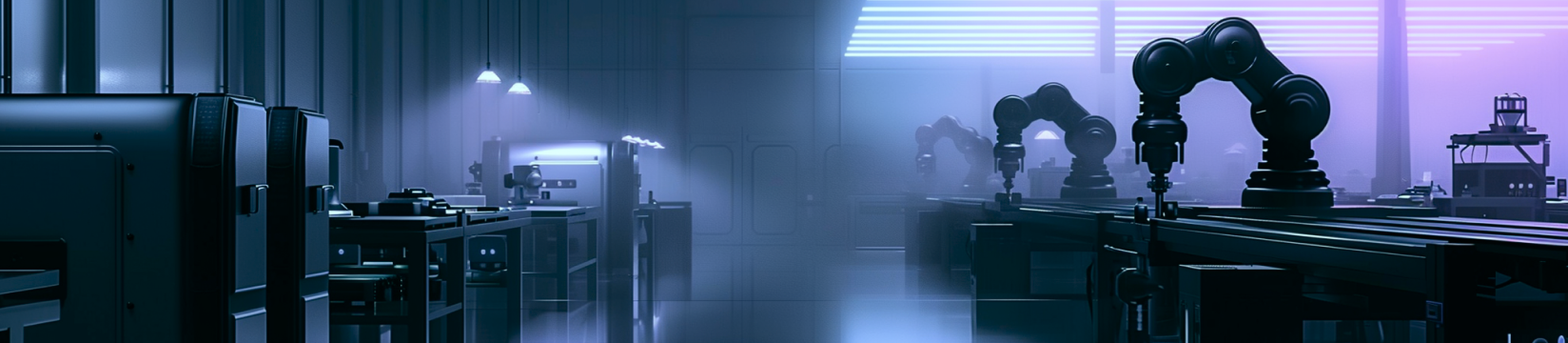
Resilience
One of the main direct benefits will be to improve the decision-making process with real-time data, driving better operational efficiency and quality control.
Sustainability
Agility
Workforce augmentation has become critical, but the ability of manufacturing and production processes to keep pace with changing industries is equally as important. Despite recent technological advancements, many manufacturers still struggle to make the most of these changes. In order to bridge the gap between current operations and the envisioned future, they must first address how to expand and improve existing systems.
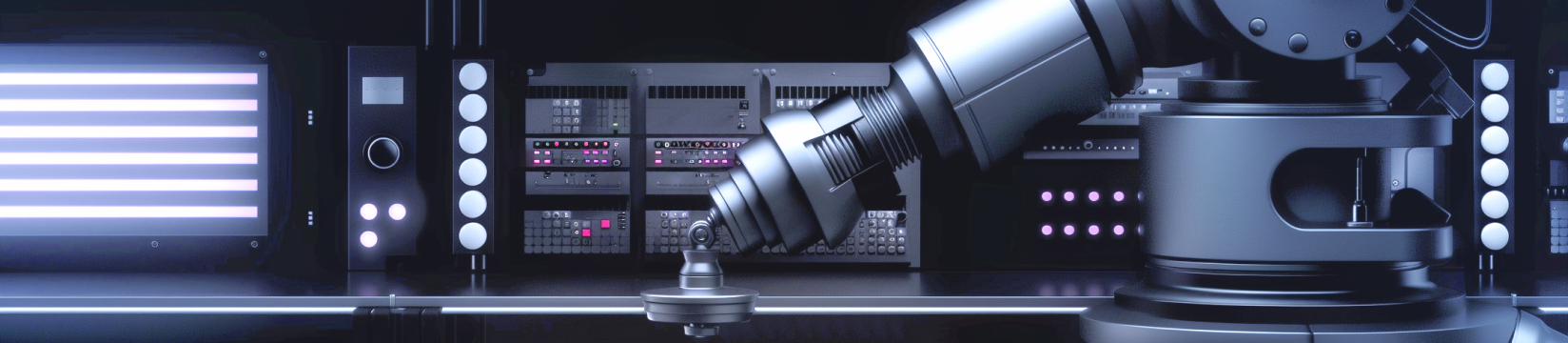
Culture
Decision-making
Digital twin technology is a major component of this approach and is focused on sequencing and organizing operational activities. These use historical and real-time data to adapt to changing demands and support modular and scalable production lines.
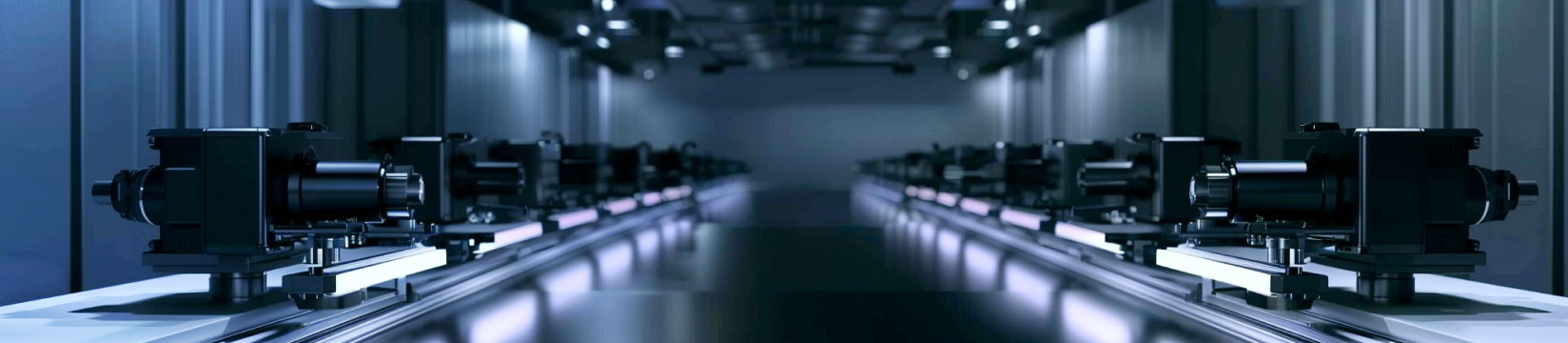
They solve complex problems and improve decision-making outcomes using simulations and computational models with intuitive, insightful, and interactive interfaces. They can facilitate virtual factory designs and simulate human-robot interactions and production launches to pinpoint potential issues before physical implementation.
They will include a combination of digital twins, AI, and virtual simulation tools that allow for custom production workflow modelling and optimization.
Adaptive
To ensure success, SoftServe offers a comprehensive suite of tools and expertise designed to enhance the scalability and adaptability of manufacturing systems. There are also an array of tools and solutions designed to bolster the resilience of supply chains.