Your Legacy Equipment Can Slow Your Digital Transformation
Digital transformation in business builds a competitive advantage by continuously incorporating tech at scale to improve customer experience and lower costs. During the past several years, it’s gone from being an optional process to a mandatory requirement for many companies.
In discussing digital transformation, IT systems modernization becomes the topic. An organization’s physical equipment needs to be digitalized as well since it can pose a significant challenge to processes. A major part of such legacy equipment is represented by various analog or disconnected gauges, meters, or other devices designed to measure certain conditions.

According to a recent survey, approximately 30% of equipment of U.S. and E.U. manufacturing companies can be considered legacy. Indeed, more than a third of respondents reported the costs of downtime due to unreliable legacy equipment at $12,701-$31,750. Read on to learn more about the challenges legacy equipment poses to businesses — and how this equipment can be digitalized today.
We’ll cover the challenges legacy equipment poses to a business and how this equipment can be digitalized today.
Legacy equipment: An obstacle to progress
Most legacy equipment, such as gauges or meters, weren’t designed to analyze the raw data at the edge and transfer it to the outside world. That’s why sensor data are gathered manually in many industrial facilities, which is highly inefficient.

Moreover, not all gauges can be easily and frequently accessed by humans — some assets can be placed in harsh or even hazardous environments, such as in some chemical manufacturing facilities. Others can be located at remote sites as used by energy or mining industries.
In this era of business digital transformation, many companies digitalize their IT infrastructure and optimize operations. However, legacy equipment cannot often connect to modern digital systems, making it difficult to integrate with newer equipment or software. Without access to detailed data, businesses may struggle to identify existing problems with their equipment, identify areas of potential improvement, and optimize their processes.
Overcoming the digitalization challenges

Digital gauges
The usual way to upgrade your legacy analog gauges is to replace them with digital versions. There are many wired and wireless options on the market today offered by various providers.
Wired digital gauges can transfer the value readings with the electrical output signal, while wireless meters use specific types of connectivity such as Bluetooth, LoRa, or others. Digital gauges provide continuous monitoring and a physical interface for manual readings. The prices for the wireless versions are in the moderate range, and a bit less for wired versions.
From the other perspective, replacing legacy gauges with digital versions modifies the existing system and is often not technically feasible.

Robots
With the recent advancements in robotics, it’s now possible to use robots for data reading from different equipment in industrial facilities. With more and better options becoming available on the market, businesses can autonomously collect data from multiple devices in one facility.
Although this approach doesn’t modify the company’s existing system or require wiring, prices for this solution are high. Also, deploying robots is complex and requires initial fine-tuning in the specific environment they’re meant to work in to ensure their desired behavior.
Finally, robots can’t be deployed in every facility because they can interfere with day-to-day workers or the machinery workflow.

Autonomous cameras
By leveraging TinyML, a form of machine learning that allows models to run on smaller, less powerful devices, SoftServe’s R&D team is developing a unique solution that can read the data from different legacy equipment, including gauges, meters, and LED light indicators.
By placing these smart devices in front of older equipment, autonomous data monitoring can be achieved. Our battery-powered solution collects data using a specific frequency and transfers it wirelessly. These devices can monitor several gauges at once, which is especially useful for digitalizing outdated control panels.
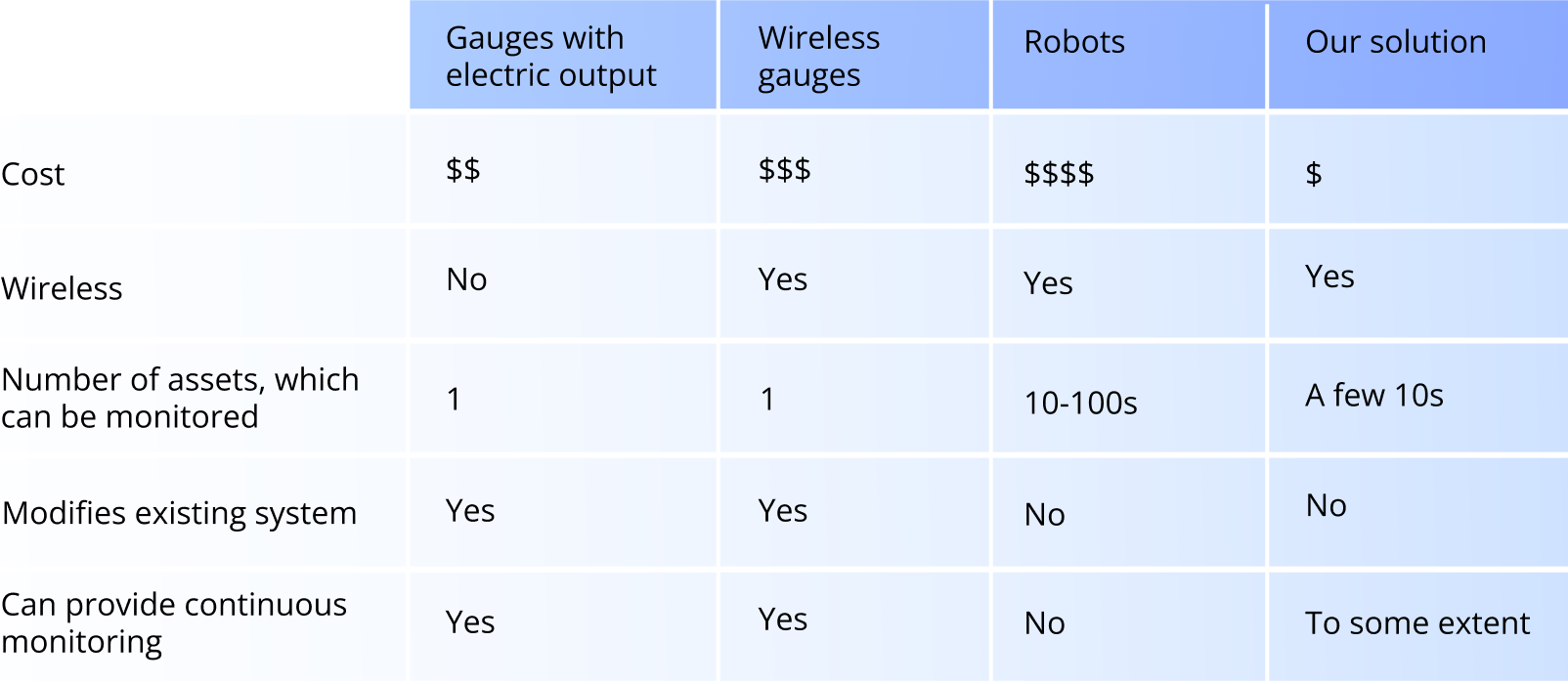
Table 1. Comparison of different options for legacy equipment digitalization
With this remote data reading, your company can implement an accurate, efficient, affordable, and convenient monitoring and reporting system. Retrofitting legacy machines and equipment with TinyML allows businesses to add intelligence to any older device without modifying the existing system.