Digital Twins: You Can’t Do It Alone
After spending a couple of decades digitizing the physical world, industries like manufacturing and energy have embraced digital twins to improve how their business runs before putting it into operation. Other industries using these virtual models to accurately reflect business processes through analysis, performance, and improvements include telecommunications, agriculture, and retail.
While digital twins date back to the “living models” of NASA’s Apollo missions during the 1960s and product lifecycle management in manufacturing during the 1980s, recent advancements in software technologies accelerated the development and adoption of digital twins by technology leaders.
Driving the case for digital twins is the need for businesses to deliver technology to solve business challenges.
A clear strategy, though, must be put in place by tech leaders and IT to capitalize on the benefits of digital twins — to extract the most value, while also integrating technology into all aspects of business operations as part of true digital transformation.
It’s also important to build a strong technology foundation and ability to drive future initiatives by using artificial intelligence (AI), machine learning (ML), internet of things (IoT), cloud, and automation. These technologies underpin digital twins and deliver the right capabilities for the right outcomes.
Navigating digital twins
Digital twins are a virtual representation of real-world entities and processes, at a specified frequency and fidelity. Digital twins:
![]() |
![]() |
![]() |
![]() |
Transform business by accelerating holistic understanding, best decision-making, and effective actions. |
Use real-time and historical data to represent the past and present and simulate predicted futures. |
Drive effective customer engagement and cross-team collaboration using virtual 3D assets of real facilities or other physical assets. |
Build self-optimized autonomous systems. |
For nearly 20 years, organizations tried to create digital versions of their assets to perfect performance and minimize defects. However, back then, the technical structure of digital twins — sensors, connectivity, compute, and storage — necessary to collect, analyze, and model data was beyond reach for most.
With IT advancement, digital twins proliferated, essentially democratizing use and application across all industries. According to IDC, 52% of surveyed resources and construction companies have at least experimented with digital twins, while 40% of manufacturers have some experience with the technology. The figures are positioned to increase with time.
Digital twins in action
Many new innovations begin with big promises but deliver limited results. Many organizations exit the digital twins trough of disillusionment into an upslope of enlightenment and are well positioned to reap significant rewards.
The applications of digital twins are boundless and grow, such as digital twins of products, digital twins of operations, digital twins of customers, and digital twins of supply chains. These simplify asset management and maintenance by replicating exact twins of assets, people, and processes.
Some of the most common and practical applications of digital twins include:
![]() |
![]() |
![]() |
Monitoring |
Analyzing |
Predicting |
![]() |
![]() |
|
Prescribing |
Adapting |
One or more of these applications come into play in a digital twin. The key is for you to decide the goal of any given digital twin and use the right applications to achieve your goals.
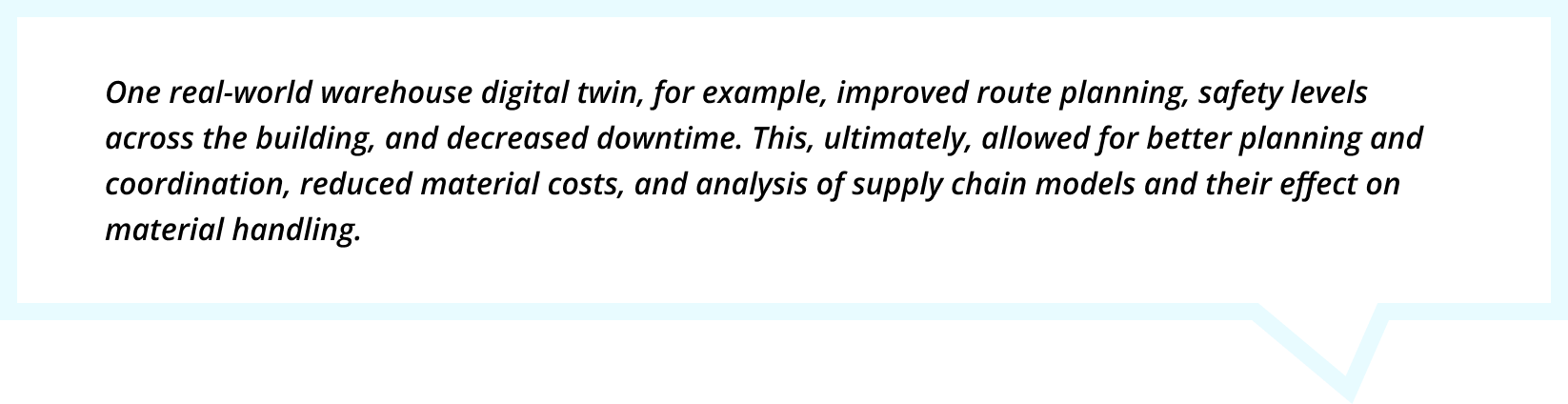
Digital twins use cases
Real-world use cases of digital twins pave the way for the digital enterprise.
For example, according to the same study cited above, 35% of Forbes G2000 companies plan to deploy digital twins by 2027 to improve their supply chain orchestration. Similarly, 40% of manufacturers plan to integrate digital twins into their products and production processes. What are the digital twins use cases driving operational efficiency increases in these verticals?
ManufacturingManufacturing is one of the most common industries adopting digital twins. Consider this use case that shows digital twins in a manufacturing environment.
The life of any electric motor starts from design. Engineers create a prototype through physical modeling to test its parameters through simulation or the simulation twin of a future asset like an electric motor. Once that motor is produced and installed, it’s critical to monitor its status. This includes reading torque, voltage, temperature, vibration, and measures linked to a dashboard or a 3D visual representation of the motor. It stands for the status twin of a physical instance.
Throughout this process, sensor-generated data is collected from a motor or even many motors of the same type. It’s possible, then, to build a model that predicts failures and fosters overall equipment effectiveness by reducing downtime through predictive maintenance. This is called the operational twin of an asset (an electric motor).
Supply chainAnother practical use case is digital twins of supply chains. The coronavirus pandemic revealed delicate supply chains that easily broke. Digital twins of a supply chain provide significant opportunities for optimization and resiliency.
Consider that every digital supply chain initiative starts with the collection of information about supply, inventory, production, orders, and consumers. This gives those businesses real-time visibility of an actual supply chain to forecast supply chain dynamics. The data foundation lives in dashboards and forecasting models of a supply chain at the organizational or process level.
Simulation twins offer optimization models based on criteria to perform “what-if” analysis, mitigate risks, or suggest the best supplier based on cost and time to market. The more complex a scenario, the more you benefit from using digital twins.
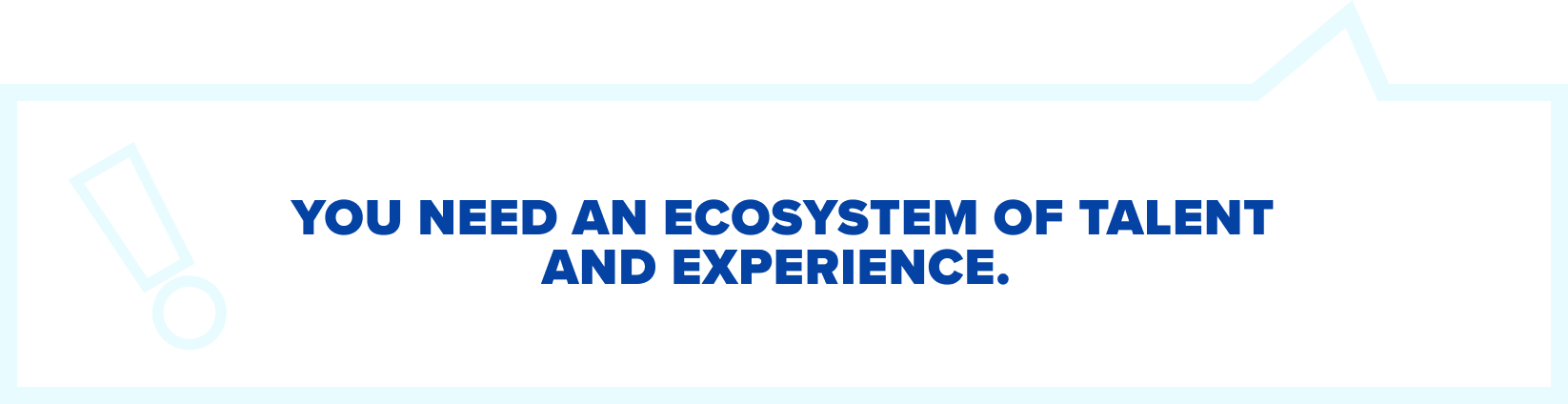
![]() |
![]() |
![]() |
![]() |
Trusted consulting and technology partners with domain ability to collaborate with your intimate industry knowledge. |
A partnership that implements battle-tested technology, frameworks, and accelerators proven in real-world applications, and applies advanced technologies to solve complex business problems. |
A technology partner with a rich, global bench of teams, authoritative in deep technical skills like data, AI, ML, IoT, cloud, and automation. |
A partner who ultimately provides technical strategy mapping for a clear understanding of your business needs. |
Conclusion
With innovative technology, missteps or ill-conceived — even inadequately-funded — projects dampen initial enthusiasm. Depending on your industry, whether it’s manufacturing or automotive, energy or retail, or smart cities and government, and your organization’s size, there are likely hundreds, if not thousands, of various asset types and equipment. For you to create digital twins of them all will take years. It’s necessary to keep a long view in mind.
Yet, the market is moving fast, and the digital twins space is rapidly maturing. More tools and vendors enter the market all the time. This can cause confusion during your digital twins journey.
The primary goal is to gain clarity on organizational and technological challenges and set the right priorities for getting business value. However, that’s not easy. Especially when digital twins initiatives span multiple departments and involve a variety of stakeholders along the company value chain.
Your organization will need to address this head-on to create opportunities. Otherwise, without urgency, you will be left behind. While your organization will have to work around events that can’t be changed, using old ways of doing things won’t cut it anymore, and you will fall behind competitively.
No matter where you are along your digital twins journey, make sure you travel it and invest with confidence. Advocate for a collaboration with a trusted partner to deliberately uncover and deliver the needed solutions in your space to ensure digital twins success.
Let’s talk about how SoftServe's guidance with digital twins will help you seize new opportunities to accelerate your business productivity and automation and mitigate risk and increase efficiencies.
Read the next article of this series about digital twins and the industrial metaverse.