Uncovering the Reality of Manufacturing Processes with Process Mining
One of major challenges of manufacturing process optimization is uncovering the current state of a client’s manufacturing processes. There can be multiple representations and diagrams that describe the process “as designed,” but not the factual one. Available process documentation is often fragmented, incomplete, and out of date.
The challenges of traditional process optimization
To generate an accurate process model for our client, we analyze all available documentation and begin the process of clarifying, interviewing, and observing by hosting process mapping workshops. During traditional value stream mapping (VSM), consultants follow sequential events in work processes with a timer in hand to record all value-adding actions. As process optimization consultants, we have encountered a couple of problems with the VSM approach:
- VSM is time-intensive and requires collaboration with production floor workers, taking time away from their regular tasks.
- COVID restrictions can prevent traveling to the remote production location and observing the process.
- VSM only produces a static snapshot of process flows.
- Data collection is restricted to a limited period of observation.
- VSM delivers a high-level end-to-end overview, but more detail is required to optimize the entire workflow process
- VSM maps both material and information flow, but it is difficult to map information flow with VSM due to advances in data processing technology.
After mapping is completed, we needed an additional set of process data to complete the model. Because of functional silos across organizations, this data is not always available. What’s more, every department can define key metrics differently. Enterprise Resources Planning (ERP) systems store a lot of process-related data, but one cannot easily find trends and patterns in information stored in hundreds of tables. Scattered records make it difficult to correlate process instances (e.g., a single production order) with activities to fulfill it.
Digital tracing with process mining
The challenges of traditional VSM can be avoided by iautomating process modeling.
Modern manufacturing machinery can collect highly detailed information from event logs about completed operations and transmit it back to data storage. Those records are time-stamped and correlated with process data in information systems like enterprise resource planning systems, manufacturing execution systems, and warehouse management systems. If every action in the manufacturing process is reflected in a trustworthy, complete event log and recorded in digital form, it is possible to recreate an accurate process model out of multiple historical event records.
On top of that, all process-related metrics are measured based on event records. This provides an actual snapshot of the process performance, unlike metrics collected by traditional means.
The family of techniques and methods used to discover, monitor, and improve real (not assumed) processes from event logs are referred to as process mining.
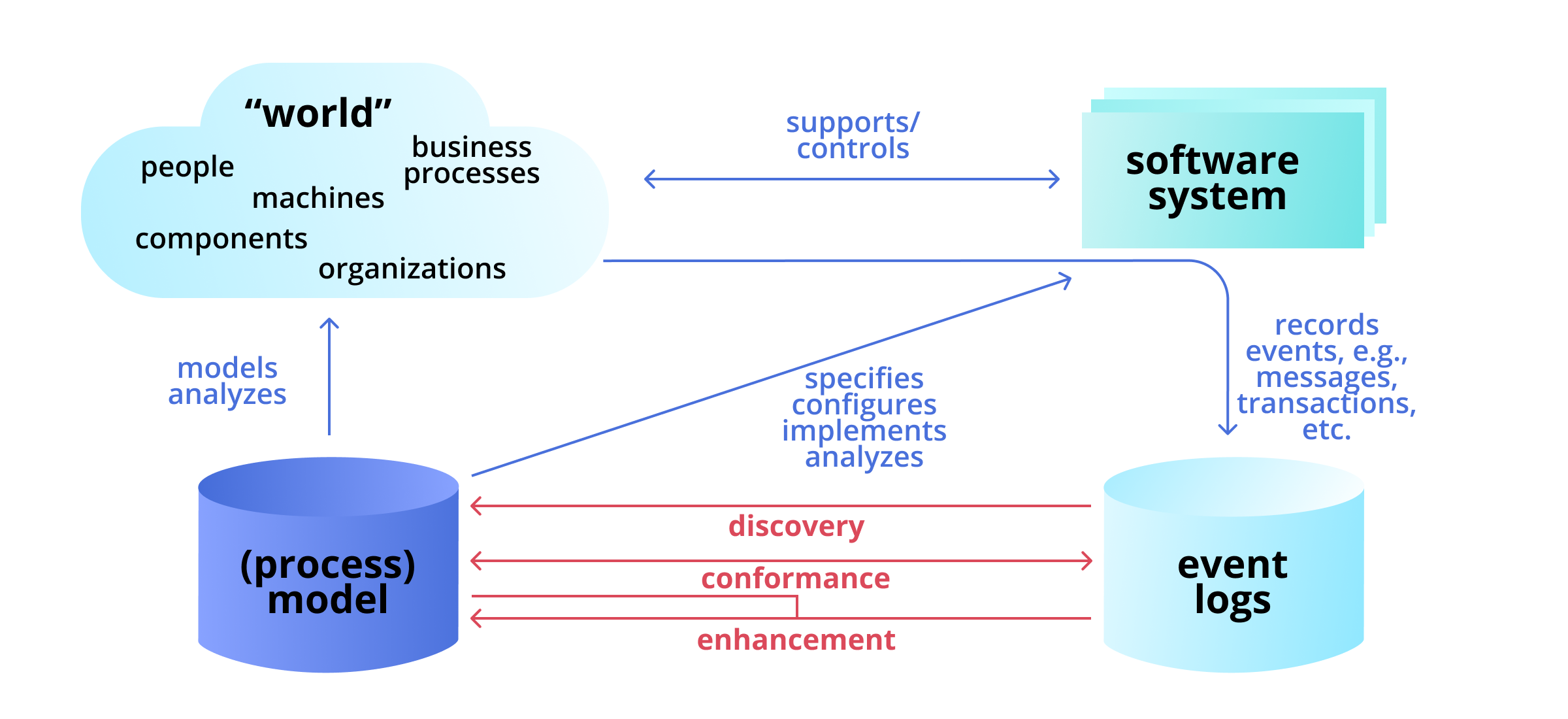
SoftServe quickly realized the advantages offered by process mining. Process mining decreases the time required to generate a process model and allows precise, reliable metrics calculation. With process discovery, we can more quickly find process waste caused by defects, overprocessing, and delays. We are excited about the potential of this new process discovery technique, and we received promising results while partnering with Celonis, a leading process mining technology vendor.
Reimagining Process Model Optimization
Regardless of the method used to map the value stream and generate the process model, the goal is to understand the real state of manufacturing operations. When the actual state of operations becomes clear, the next step is to identify process inefficiencies.
Combining traditional VSM and process mining techniques unlocks new methods for process optimization. By comparing process models dynamically generated from real data (“as realized”) with VSM-model (“as designed”), analysts can reveal fundamental roadblocks to fully optimized processes, including:
- Bottlenecks
- Process variation
- Non-value adding activities
SoftServe developed a methodology for process improvements that combines dynamic models produced by process-mining and available static models. Our method is inspired by SoftServe digital journey concept, a model for how enterprises can achieve digital transformation.
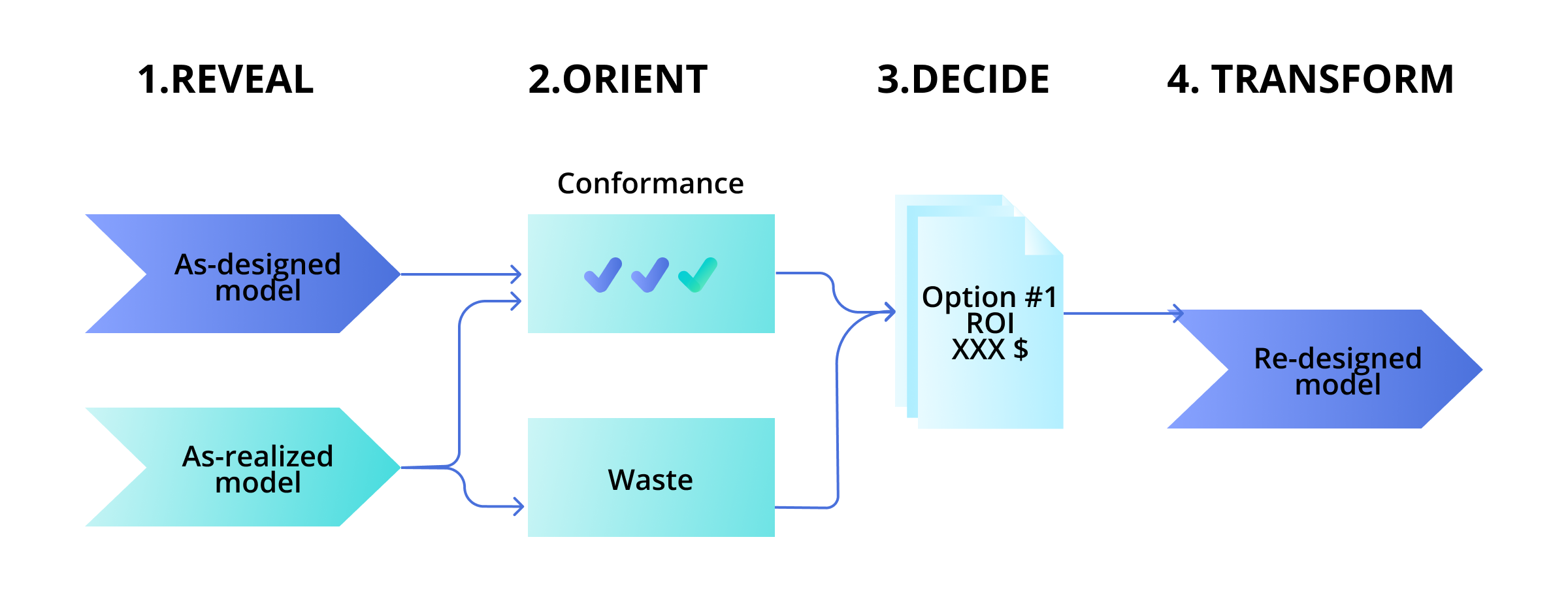
- Reveal: The reveal phase requires setting up process mining tooling, data extraction, and generation of “as realized” process. It also includes assessment and evaluation of available process documentation and process maps produced by VSM methods, if they are available.
- Orient: The orient phase includes diagnostics of as-realized process and how it conforms with as-designed process. Identification of inefficiencies and non-value added activities is also conducted in this phase.
- Decide: During the decide phase, we evaluate multiple potential solutions to optimize the process. Projected ROI is calculated for every proposed option.
- Transform: During the transform phase, process change is implemented and introduced as a combination of business process management and change management techniques. The existing process-mining setup is used as a verification mechanism.
While evaluating potential improvement initiatives, we prioritize those that can be scaled up to enterprise-wide applications and produce maximum ROI after implementation.
Our experience in technology-driven process improvements encompasses the following applications:
- Digital twin for remote production optimization
- Analytics platform for deviation root-cause identification
- Real-time asset performance monitoring and visualization
- Remote assistance using augmented reality
- AI-powered optical inspection
- Energy and waste optimization through predictive analytics
Companies are urgently increasing their investments in smart manufacturing initiatives because of market conditions caused by COVID-19. To thrive in the "new normal," organizations will require even more investments in smart factories. As an experienced consulting partner in the deployment of AI/ML, big data, and cloud manufacturing technologies, we position our clients for success in a rapidly changing industry.
LET’S TALK about how SoftServe can help you optimize your business processes using the best of VSM and process mining.