At the peak of COVID-19 pandemic SoftServe collaborated with a 150-year-old western European company that specializes in food production. Our client is vertically-integrated and operates production facilities in multiple European countries. The company constantly innovates across the value chain and maintains close ties with partners and suppliers to develop a technologically-driven ecosystem. The company prioritizes lean manufacturing practices and focuses on operational efficiency.
Due to changes in market conditions and industry deregulation, the company’s profit margins were deteriorating. The company launched an initiative to transform business processes such as finance, legal, process management, onsite administration and controlling, purchasing, quality, EHS, HR, and more.
Our client’s primary goal was to increase the overall efficiency and throughput of the existing processes using industry best practices and digital technology. A secondary objective was revealing additional functional areas as candidates for further improvements.
The COVID-19 outbreak was a triggering point for action that prompted collaboration with SoftServe. The company had only a high-level knowledge of the whole set of internal supportive processes. Methodology for documenting, assessing, and optimizing processes was lacking.
SoftServe consulted and advised on the methodology and approach suitable for the challenge. Additionally, the decision-making techniques for process optimization options were developed and tailored to meet customer context. SoftServe allocated a cross-functional team of business process experts and business function SMEs.
During a series of workshops and deep-dive assessments, the team was able to:
- Scope business functions using a value chain model
- Define functional areas and high-level processes that required immediate attention
- Define and tailor our approach to operational efficiency
The proposed approach included a plan of main activities and a set of qualification criteria to grade optimization potential.
Because of the vast number of processes and time constraints, it was not possible to model every individual process and evaluate the optimization potential of each. SoftServe proposed a top-to-bottom approach to segment the whole set of processes into a finite set of clusters. The clusters were then evaluated and prioritized by their potential for optimization.
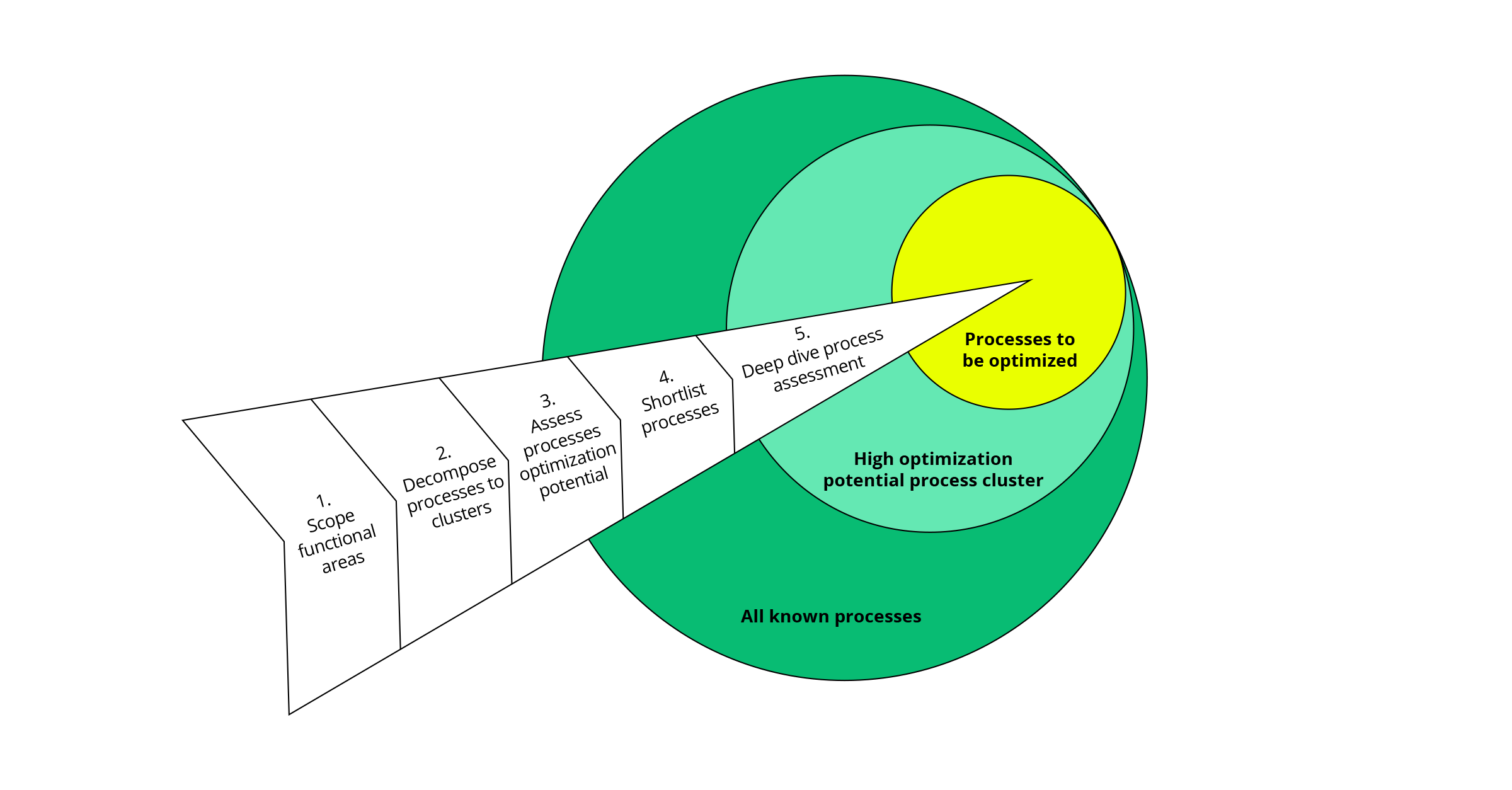
Our optimization potential assessment included the following steps:
- Modeling process and estimating labor cost footprint of the process instance
- Process complexity assessment
- Feasibility study for process avoidance
- Feasibility analysis for process automation
- Feasibility analysis on additional cost reduction options
As proof of value of the proposed approach, SoftServe executed all advised activities in one supportive process.
The proposed approach was based on the operational efficiency framework previously developed by SoftServe, tailored to the specific needs of our client. Techniques for choosing process optimization options were derived from SoftServe’s internal robotic process automation practice and cost-benefits approach derived from the operational efficiency framework.
SoftServe equipped the customer with guidance, methodology, and tools to execute large-scale business processes optimization aimed at the ambitious goal of cost reduction.
The quantifiable objective was a 20% total operating cost reduction. This total cost saving was to be realized after implementing a three-phase initiative:
- Phase 1: Process elimination (5% of the total number of processes)
- Phase 2: Processes automation and redesign (25% of the total number of processes)
- Phase 3: Further optimization through other methods (25% of the total number of processes)
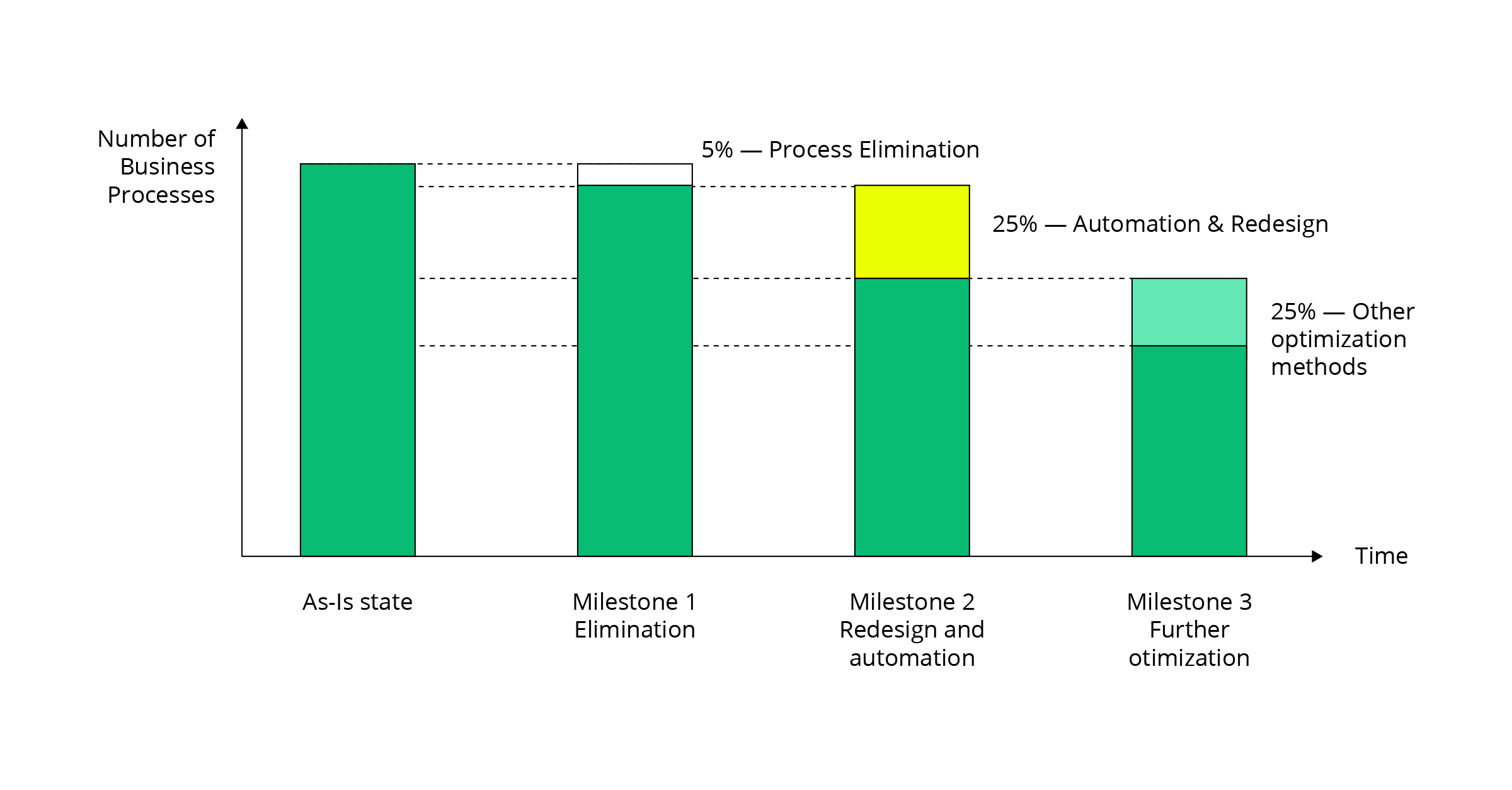
SoftServe can help maximize your company’s operational efficiency using innovative technologies.
LET’S TALK about how SoftServe can help maximize your company’s operational efficiency using innovative technologies.