Top European Food Producer Explores Robotics and Automation on the Vertical Farm
A story of autonomous farming containers and affordable custom robotics
Our customer is a top European food producer with exceptional agricultural practices and a solid commitment to excellence and sustainability at every step in the value chain. They’re known as innovators. Therefore, it wasn’t surprising when they began, as they describe, “to tackle the challenges of agriculture with new technologies."
After thoroughly analyzing disruptive agriculture technologies, our customer pursued advanced vertical farming techniques. However, they quickly discovered that growing their product in vertical farms would be significantly less profitable than continuing to grow it as usual—on free land.
The question was asked: Could the production expertise and skills gained in their traditional farming practices help them step into a new business—growing new produce types in vertical farms located close to their consumers?
The answer: Yes, but only if the operating costs of growing new crops in the vertical farm are lower than growing them using traditional agricultural practices.
Running vertical farms on a production scale can be expensive if it involves manual operations. Dedicated resources performing routine tasks are cost prohibitive in countries with high salary rates. Therefore, our client decided to invest in a research and development (R&D) initiative to automate manual tasks inside the vertical farming container, making it economically attractive.
They chose SoftServe as their strategic innovation partner for this project and made SoftServe’s robotics and engineering team their R&D team.
Why SoftServe? There aren’t many companies like SoftServe, with a proven record of successfully delivering complex end-to-end solutions involving both hardware and software components—from advisory through prototyping to the actual product launch and support.
Typically, R&D for a robotics project is costly and out of reach for many organizations. SoftServe designed, tested, prototyped, and built the robotics hardware and automation platform remotely. Our experts used a robotics simulation to gain early feedback that allowed us to reduce the number of physical prototype iterations—significantly reducing project costs.
It was a great success.
Join me as I briefly discuss vertical farming, walk through the SoftServe Vertical Farming Robot Project, and explain why designing hardware remotely is a big deal for manufacturing companies.
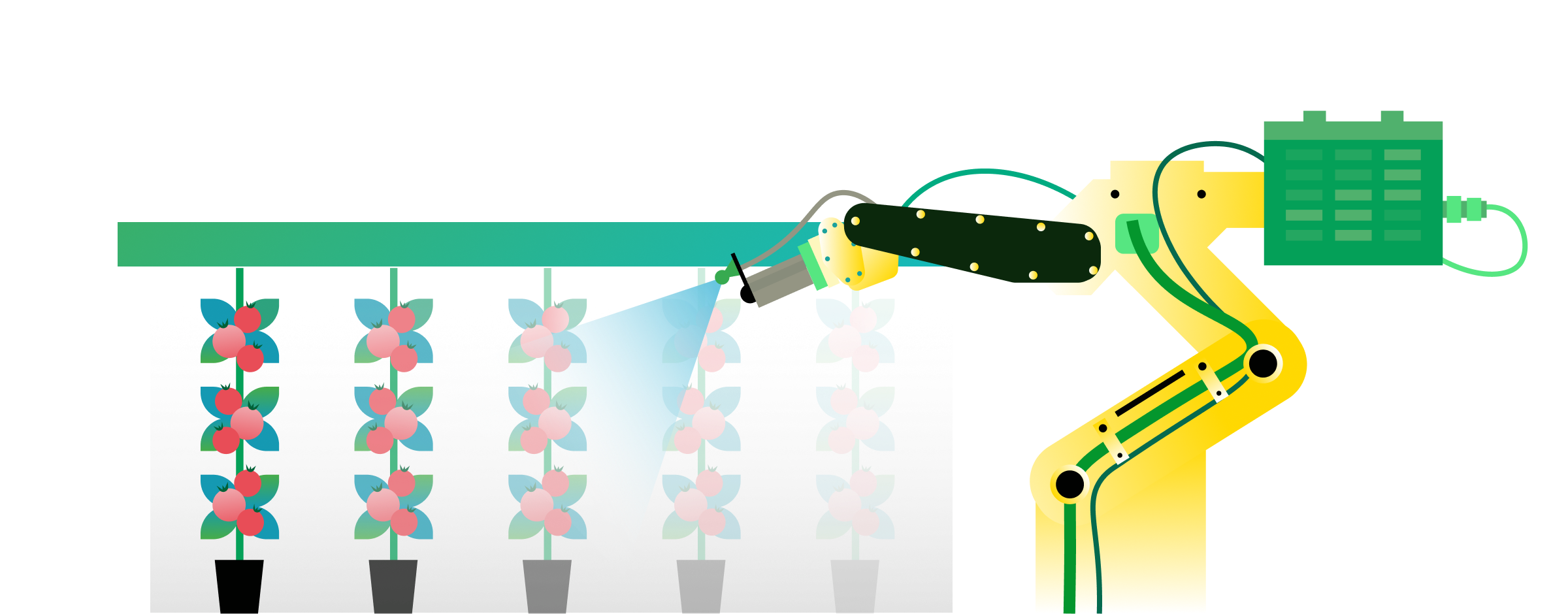
A little about vertical farming. Why isn't everyone exploring this option?
Vertical farming is a way of growing food indoors, typically in multistory buildings stacked with growing containers. You can almost guess the advantages, like:
- Expanding the range of products grown, particularly in a changing climate
- Reducing the environmental impact
- Limiting the use of pesticides or herbicides
- Creating viable farms in remote areas where crops can’t grow
Considering the advantages, why isn't every food manufacturer using vertical farming for at least some crops? Simply put, running a vertical farm is significantly more expensive than traditional farming.
There are many reasons why it's so expensive, and the vertical farming Wikipedia page provides an excellent overview of the advantages and problems.
In our customer’s case, the business model requires their vertical farms to be in relatively high-priced living areas, making hiring the people to run the farms expensive. Vertical farming containers without advanced technologies are labor intensive, requiring manual seeding, transplanting, and harvesting.
SoftServe’s robotics and engineering experts partnered with our customer’s agricultural gurus to design and build robotics and advanced software technologies for the selected configuration of the vertical farming container, automating as many farming tasks as possible. The intended result is to reduce the costs of personnel needed to run the vertical farm and make growing crops in the vertical farm profitable.
The SoftServe vertical farming robot
How it works and why it’s so revolutionary in agricultural practices.
The goal of the ongoing project is to design a custom robot to achieve full-scale automation inside the vertical farming container, so it becomes an autonomous unit entirely controlled by technology. Once completed, vertical farming becomes a more viable farming option.
SoftServe built a pre-programmed robot in simulation consisting of a static platform with a movable robotic arm. We simulated how the hardware behaves in the given environment to properly test how it works before building the hardware itself. The current robot:
- Scans the plant using proper cameras and computer vision, defines its size, temperature and moisture level, takes a photo, and sends it to cloud storage.
- Performs transplanting operations.
Each iteration of the design was focused on:
- Finding the best ways of moving the robot in a restricted space and following safety regulations without impacting the environment itself.
- Ensuring the arm is stable enough to reach out of the container's high walls.
- Designing the proper hardware solution allowing the robot to pick up the seedlings without damaging them and reliably fix them into the vertical panel.
- Combining different camera configurations and lighting setups to achieve proper photo resolution.
The next iteration is about achieving full-scale automation, including seeding and harvesting.
Although this project is just one part of the bigger vision of making the vertical farming business even "smarter" using AI and ML technologies, it's one of the most crucial first steps.
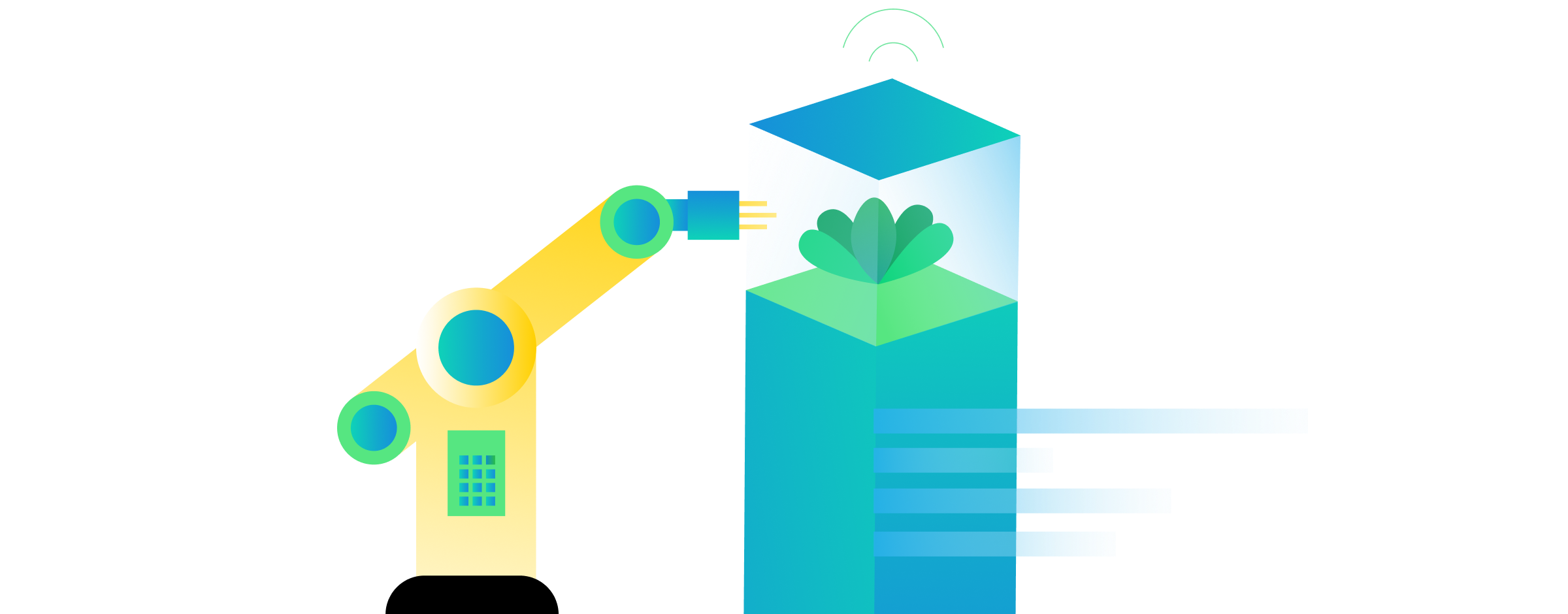
The vertical farming robot’s value
The team came up with a custom solution that can easily plug into the existing container environment, prove its feasibility within the known set of constraints, and generate the following values:
- Provide a prototype for justifying investments in the vertical farming business in target markets with high salary rates.
- The automated transplanting process minimizes the overall time spent by the operator inside the container.
- A combination of reduced labor costs and other factors (such as solution scalability and automation of different processes) makes our solution profitable over a few years.
- Enabled new cost-efficient operations that were previously physically impossible.
- In traditional farming, there was no way to take photos of each plant and observe its growth at different stages. In the vertical farm, this is done with image recognition and light control with a cost of only 1 cent per salad to take a picture daily throughout the plant’s lifecycle.
- Reduced the farm’s energy consumption by doing fast plant diagnostics based on the plant snapshots, which allows for keeping the robot in an energy-saving mode longer.
- Enabled continuous and accurate plant data collection.
- According to the test results, the level of achieved precision in plant detection and size measurements is more than 90%.
Robotics projects done remotely. The answer to making customized robotics more affordable
We designed, built, and tested a solution, including hardware and software components, entirely from scratch while running the project remotely. This is a big deal for manufacturing companies.
Running this project with our client through purely online collaboration allowed the most experienced and skilled people from both sides to work on the tasks. As you would expect, there were challenges along the way, but together we found ways to work efficiently by using collaboration tools like video and 3D simulation.
Designing and testing the vertical farming robot was a yearlong process that would have been impossible for the customer or SoftServe if engineering resources had to be on-site for an entire year. When the robot is ready to be piloted, only a small team of engineers and the robot need to travel, allowing for significantly reduced travel expenses for such a challenging and innovative project.
Research and development of hardware solutions, like robots, was out of reach for most manufacturers due to the number of iterations done during research and the cost of in-person collaboration. SoftServe’s experience and expertise in robotics allowed us to design the custom robot remotely and reduce the number of physical iterations needed, significantly reducing costs. Custom robotics is now available to any manufacturer. The possibilities are endless.
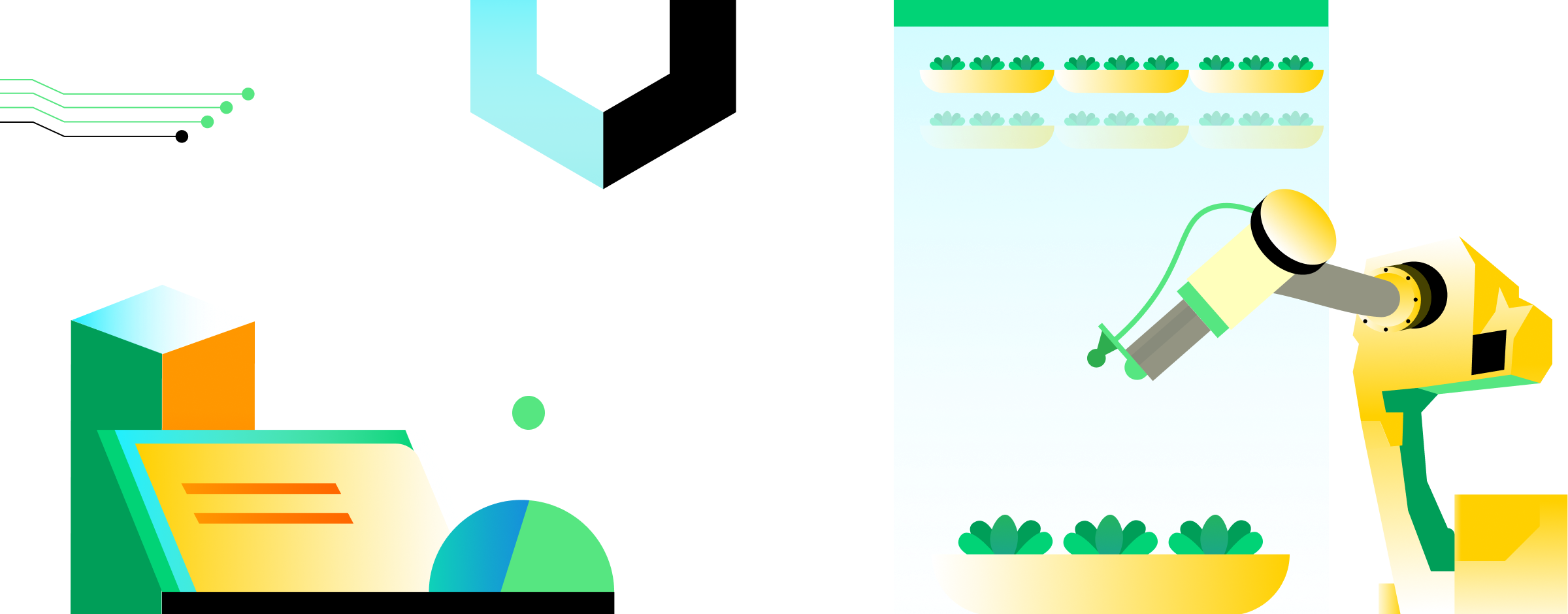
Final thoughts—unlocked opportunities
The superior teamwork used to design the vertical farming robot also unlocked new opportunities for this client, such as:
- Applying capabilities created in the scope of this initiative in other business areas (i.e., using computer vision for better weeding practices).
- Exploring new markets with high labor costs for business expansion.
- Using gathered plant data in different ways across the enterprise, (e.g., to simulate the plant's behavior over time with the help of a "digital twin," figure out the most profitable crop breeding and cultivation techniques, and proactively impact the growing process).
The SoftServe Vertical Farming Robot Project was just the beginning of our client’s journey to entering a new business, scaling it, continuously improving it, and inventing more disruptive solutions. We’re proud to help them innovate and build new agricultural breakthroughs.
SoftServe is a trusted partner for this client and has worked on several of their digital transformation projects. Here’s an overview of another successful project, ADVANCED AUTOMATION WITH ROS 2 FOR INDUSTRIAL PROCESS CONTROL SYSTEMS (PCS).
Want to learn more? Contact a SoftServe expert.