Data-Driven Energy Optimization: Making Cuts Without Sacrifices
Reducing your energy use is non-negotiable, but it doesn’t mean that you need to compromise on quality.
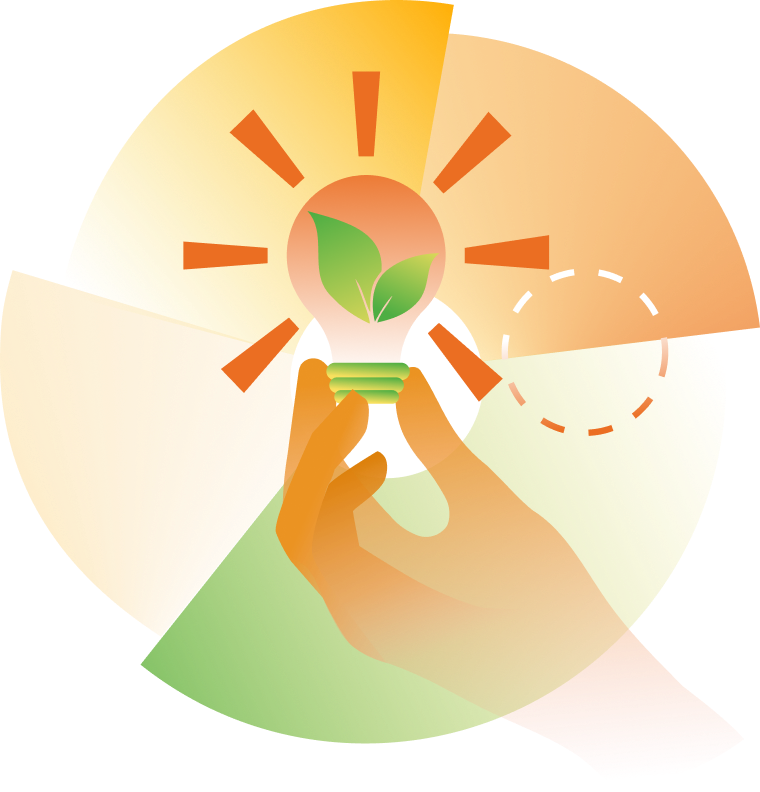
The need for green production through lower energy use has never been more apparent, but inferior products are a non-starter. While there is some play in the dynamic of quality and efficiency, many manufacturers struggle to lower their energy consumption while maintaining excellent quality.
The problem is that you might not actually know how much energy you need to efficiently satisfy your own production standards. With so many factors at play, it’s impossible to know which one matters—much less optimize for it—using traditional methods.
You need a different level of insight to discover how you can make cuts without making sacrifices.
Understanding the potential
When a client approached us to collaborate on an experimental vertical farm, one of the main obstacles to competitiveness was the farm’s energy usage. Leafy greens grown in containers cannot absorb sunlight, so operators must pay for what traditional farms get for free.
To tackle this problem, our client had to figure out how to use the vertical farm’s strengths to overcome its weaknesses. As it turned out, the former emerged directly from the latter: Because vertical farms are enclosed in containers and rely on electricity to generate light and heat, they provide complete control over the growing environment.
So, instead of looking outside its vertical farm to reduce its energy use, our client began asking a different question—how much energy do leafy greens need to grow well?
Listen to your products
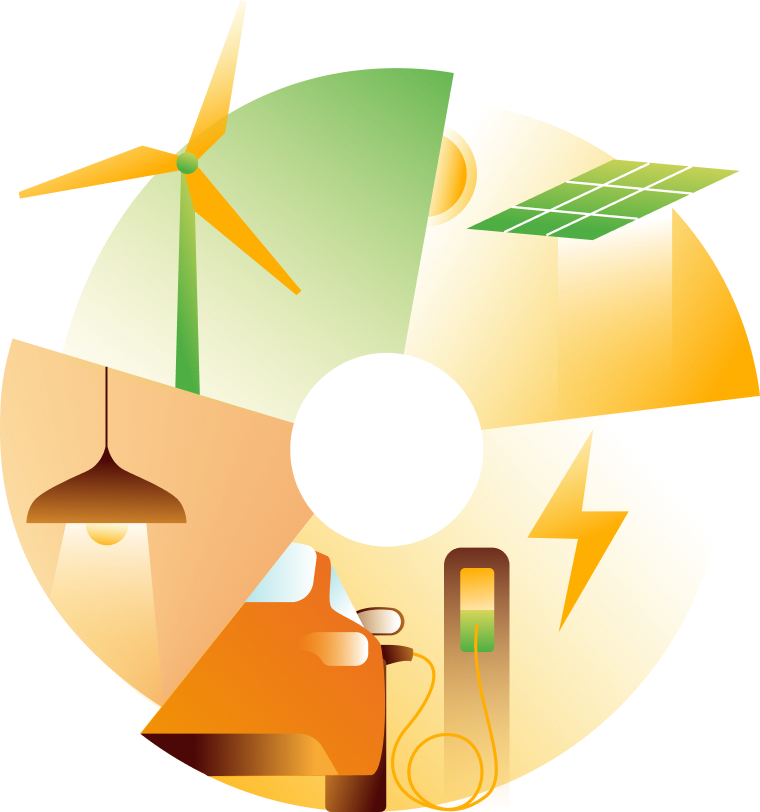
Gaining control over your energy use starts with gathering all the information about your production’s internal and external factors. Once you have that, you can begin to analyze your consumption and develop strategies to reduce consumption.
But still, discovering which interventions will work presents its own challenges. To experiment on your active production can lead to serious quality or throughput losses. And performing physical experiments at scale gets expensive fast.
What you need is a low-cost way to test out multiple scenarios without risking subpar throughput or impacting your product’s value.
Every production process can be made more energy efficient, it’s just a matter of figuring out how.
Simulation and experimentation

For our client, that began by developing a robotic solution to take a picture of each individual plant every day. Outfitted with high-speed diagnostics, the solution enters power-saving mode when not actively operating, making it energy-efficient and labor-reducing—all at a cost of just €.01 per plant for its entire lifespan.
More importantly, those daily pictures created a data stream that could be converted into a digital twin of each plant and the entire growing environment. These twins enabled experimentation without interfering with the operations of the vertical farm and opened the door to probing ”what-if” scenarios and interrogating differences in growth based on factors including type of light, space allocation, time in the cultivation area, plant breed, and nutrition.
With an effectively unlimited capacity to simulate different scenarios based on energy use and plant growth, our client is on its way to reducing its energy consumption to an absolute minimum and achieving truly green production.
Have your data and eat it, too!
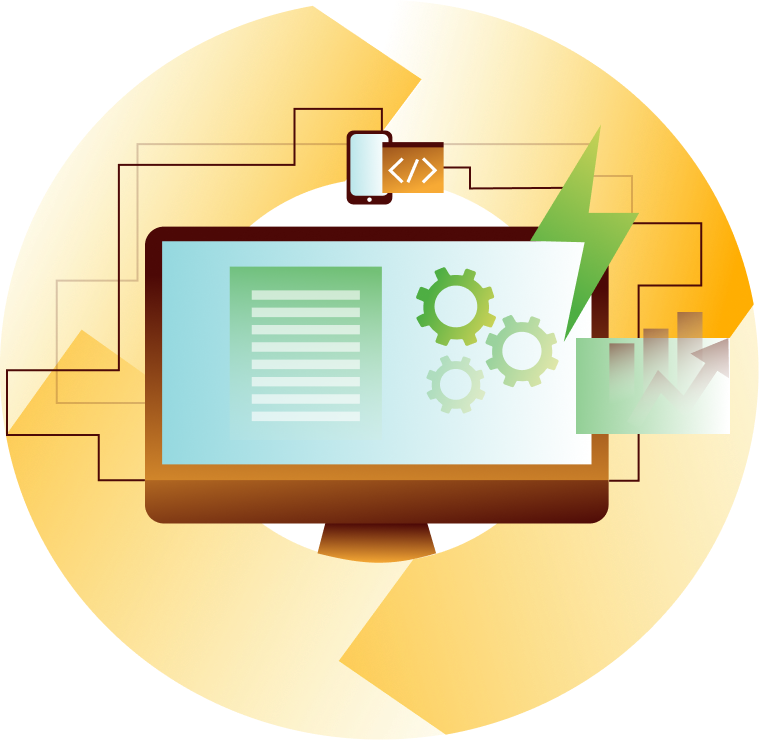
By using data analysis and integration, you can implement usage pattern detection and understand how much energy each part of your production requires.
Then you're already on the way to deploying simulation technology that can give you strategies for bringing down your energy use.
If you are interested in reducing your consumption without sacrificing quality, let’s talk!
And if you want to find out more about how we collaborated with our client, dig into the case study here.
And if you want to learn even more about data-driven energy management, read our white paper.