The Time Traveler's Guide to Digital Twins in the Industrial Metaverse
Actual time travel remains elusive — virtual time travel within the industrial metaverse is transforming modern industrial operations.
Catchy phrase to catch your attention, yes. However, it’s true.
Digital twin technologies in the industrial metaverse excel at analyzing the past to accurately predict the future. The implications of this go far beyond saving money on equipment maintenance, although that is a fantastic perk.
Digital twins alone have the potential to make industrial manufacturing practices markedly safer and more reliable with greater sustainability. The industrial metaverse brings digital twins to the next level, and the era of transformative innovation continues.
This guide takes you through projects of customers, who are either realizing or actively working on enhancing their industrial operations by leveraging digital twins.
Digital twins driving positive change
These are real-world examples of how virtual replicas are making an impact and redefining possibilities across various industries.

Fueling important industry innovations
When helping a customer explore vertical farming, a prototype robot was designed to scan each plant using proper cameras and computer vision. It defines the plant's size, temperature, and moisture level, takes a photo, and sends it to cloud storage.
The captured data is then leveraged to simulate the plant’s behavior over time with the help of a digital twin. The digital twin is used to identify the most profitable crop breeding and cultivation techniques to optimize the growing process.
The impact: Vertical farming maximizes food production while minimizing land and water usage. However, its high costs hinder widespread adoption, particularly in countries with expensive labor and resources. The implementation of digital twins will boost vertical farming popularity by reducing the need for manual labor. It will also:
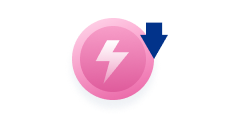
Reduce energy consumption through fast plant diagnostics and trigger resources into energy-saving mode.
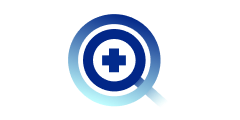
Achieve precision levels in plant detection and size measurements, optimizing growing times.
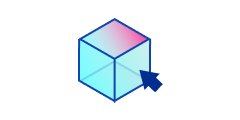
Utilize the plant data for simulations, optimizing breeding and cultivation techniques to proactively intervene in the growing process.

Avoiding industrial accidents
Visual inspection is crucial for managing offshore energy facilities like oil platforms. SoftServe's energy team developed a comprehensive AI solution for various inspection purposes, such as corrosion, coating breakdown, pipeline leak detection, cracks, and equipment defects.
By collecting visual data from cameras and sensors, implementing computer vision techniques, and training AI models, our client was able to perform real-time analysis and inspections of new images. They now find anomalies and fix issues fast before they become real-world problems.
The impact: The trained AI model analyzes and inspects new images based on data from older images and prevents any number of industrial accidents by:
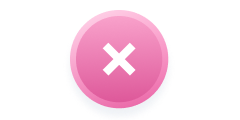
Preparing for repairs using time series images to predict future problems in different areas, units, and the entire site.
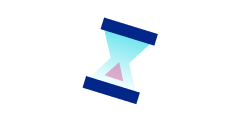
Using historical data and new images to find existing serious faults or cracks in equipment, avoiding an oil spill or another structural disaster.
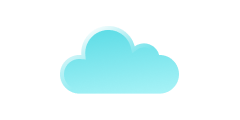
Utilizing data that considers equipment plus weather and sea conditions significantly enhances inspection safety.

Prioritizing employee well-being
Our research and development (R&D) team has done impeccable work on improving the working conditions at mining sites. They've focused on fleet management, health and safety, and sustainability using advanced technologies like artificial intelligence (AI) and machine learning (ML).
AI and ML are used to analyze health and safety conditions, including monitoring dust levels for mask recommendations, optimizing driving routes for mining vehicles, and accurately predicting maintenance needs to prevent accidents.
By integrating data from mining sites with historical and current information on equipment, weather conditions, and geological features, decision-makers can make well-informed judgments regarding present conditions.
The impact: These technology solutions are paving the way for 3D models of mining sites and digital twins. This advancement will allow:
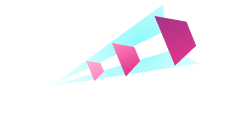
Operations teams to navigate virtually through a mining site, analyzing potential problems and dangers.
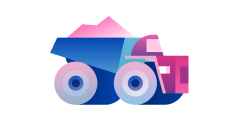
Recommendations for truck speeds that consider weather conditions, road slope, tire grip, and road degradation.
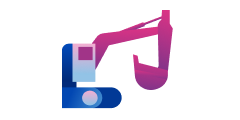
Predictions for equipment maintenance using “what if” scenarios, leveraging data from the mining site as well as past and present equipment data.

In the industrial metaverse, hosting digital twins becomes a powerful tool by creating a virtual world to test solutions or equipment fixes before implementing them in the physical world. Collaborative efforts become easier in the metaverse, and problems are solved more effectively.
![]() |
![]() |
![]() |
||
Fueling industry innovations |
Avoiding industrial accidents |
Caring for employee well-being |
||
Picture experts, researchers, and farmers sharing the virtual platform, exchanging ideas, and sharing best practices. All collectively working towards advancing vertical farming techniques. This fosters innovation and accelerates learning, speeding up the widespread adoption of vertical farming. |
Creating digital twins that leverage time series images and historical data in the metaverse provides unprecedented computational speed, surpassing previous limits. Countless “what-if" scenarios and simulations can run, enabling proactive risk assessments and emergency preparedness, reaching new levels of safety. |
AR/VR glasses can overlay digital information on a real-world mining site. Employees wearing these glasses receive real-time data and notifications about their surroundings, such as safety warnings, equipment status, or navigation instructions. All helping them avoid potential hazards to navigate the mining site more effectively. |
The examples given here are just the beginning. The potential of digital twins and the industrial metaverse to enhance safety, reliability, and sustainability in industrial manufacturing practices is immense.
Want to learn more about digital twins and the industrial metaverse? Our comprehensive white paper, "When Digital Twins and the Industrial Metaverse Converge," provides clear explanations, practical examples, and valuable resources to understanding the incredible results these technologies can accomplish together.